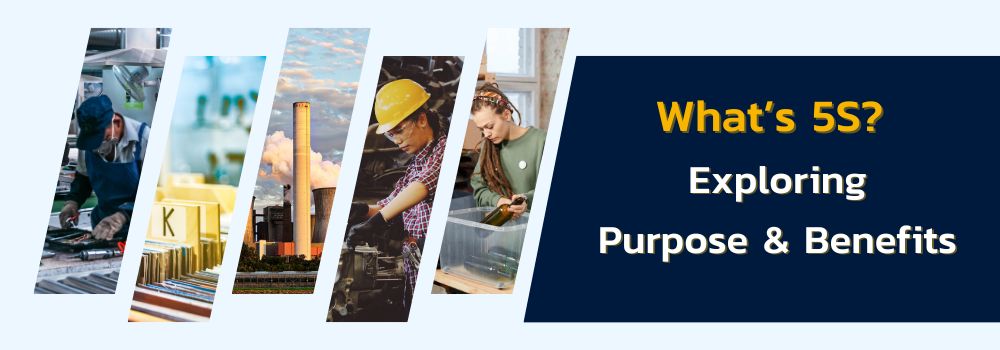
The 5S serves as a cornerstone for establishing a conducive work environment, encompassing five pivotal elements
The 5S principles are introducedto cultivate a conducive working environment and consist of five key elements: Sort (Seiri), Set in order (Seiton), Shine (Seisou), Standardize (Seiketsu), and Sustain (Shitsuke). 5S has the power to enhance operational systems and address various challenges.
Originally, the 5S was formulated to tackle prevalent issues primarily in the manufacturing, construction, and healthcare sectors. However, nowadays, they have gained widespread adoption in various other industries as well.
Seiri
“Seiri” (Sort) involves the separation of essential items from non-essential ones. This is especially relevant in high-output environments like factories, where substantial production often generates a significant amount of waste. Disorderly disposal of waste can result in difficulties when searching for specific items, potentially leading to accidents. Hence, it is crucial to promptly dispose of superfluous items.
Moreover, maintaining a meticulous inventory record, including details such as manufacturing year and quantity, is advisable. Regular audits, conducted at least monthly, help ensure effective overall management and minimize the accumulation of unused items. This proactive approach aids in streamlining operations and enhancing workplace safety.
Seiton
“Seiton” (Set in order) focuses on arranging essential items in easily accessible locations. This entails selecting an optimal placement for materials and tools required for work, considering user convenience and usage frequency. This strategic organization facilitates faster and more streamlined workflow processes.
To further enhance efficiency, it’s beneficial to establish a standardized system for placing new equipment or tools, ensuring consistency in their location. Additionally, sharing this placement information with other employees promotes a cohesive understanding of the arrangement.
In cases where a tool or equipment is shared among multiple users, a practical practice is to employ a “In Use” signboard placed within the tray during usage. This serves as a clear communication method, ensuring that other users are informed and can coordinate their tasks accordingly.
Seisou
“Seisou” revolves around the maintenance of clean equipment and ensuring a clean workplace. A clean environment fosters a mindset where work can be accomplished at any given moment. Cultivating a habit of vigilantly maintaining cleanliness is crucial.
This practice not only aids in promptly identifying equipment malfunctions and potential defects but also minimizes the risk of accidents and associated issues. It’s advisable for companies to designate an individual responsible for daily equipment and premises cleaning. This allocation of responsibility enhances the efficiency of cleaning procedures, contributing to a consistently tidy and safe work environment.
Seiketsu
“Seiketsu” entails maintaining workplace hygiene, adhering to the foundational 3S mentioned earlier: Seiri, Seiton, and Seisou. It is imperative for employees to incorporate these methodologys into their daily routines, fostering a culture of hygiene within the organization.
Furthermore, it is advisable for the company to appoint an auditor responsible for verifying and and enforce these methodologys, ensuring hygiene standards are upheld. This proactive approach promotes a sustained culture of hygiene within the workplace.
Shitsuke
“Shitsuke” involves habitualizing the aforementioned 4S for a clean workplace environment. Companies should actively promote awareness among all employees regarding the significance of adhering to the 5S rules. Additionally, they should organize pertinent activities to cultivate a shared commitment to these methodologys.

“The Purpose and Benefits of Implementing 5S”
Why implement 5S? The adoption of 5S yields numerous advantages. It fosters workplace efficiency, enhances production efficiency, bolsters organizational security, and nurtures a heightened sense of organizational consciousness among employees.”
Enhancing Work Efficiency and Increasing Production Efficiency
In an environment cluttered with unnecessary items and disarray, the quest for essential documents or tools becomes a time-consuming endeavor. Conversely, when rigorously applying the 5S, an environment is cultivated where vital items are readily accessible and returnable to their designated spots. This enables employees to concentrate on critical tasks, fostering operational efficiency.
Likewise, within production sites, adherence to 5S can yield improvements in Quality, Cost, and Delivery (QCD), representing the three pivotal elements in production control.”
Elevating Security Levels
When materials or tools in the workplace lack orderly organization, the unexpected of the accidents can be rises. Regularly equipment inspections and maintenance are essential for safe and proper operations. The 5S plays a crucial role in injury and fatality prevention, particularly in high-risk sectors such as manufacturing and construction.
Therefore, companies should prioritize the implementation of these methodologys, recognizing their significant impact on workplace safety.”
Boosting Employee Motivation
A cluttered and disorganized workplace not only elevates the risk of accidents but also contributes to employee stress. Conversely, a clean and orderly workplace fosters improved concentration among employees. Embracing the 5S can cultivate a pleasant work environment, ultimately elevating employee motivation and potentially reducing turnover rates.
In Summary
Adhering to the 5S goes beyond merely maintaining a clean work environment. It can also significantly boost employee motivation, increase production output, and elevate safety standards within an organization.
In the next blog, we’ll take a deeper dive into the practical implementation of 5S. Stay tuned to discover how to put these principles into action and witness the remarkable transformations they can bring to your workplace.