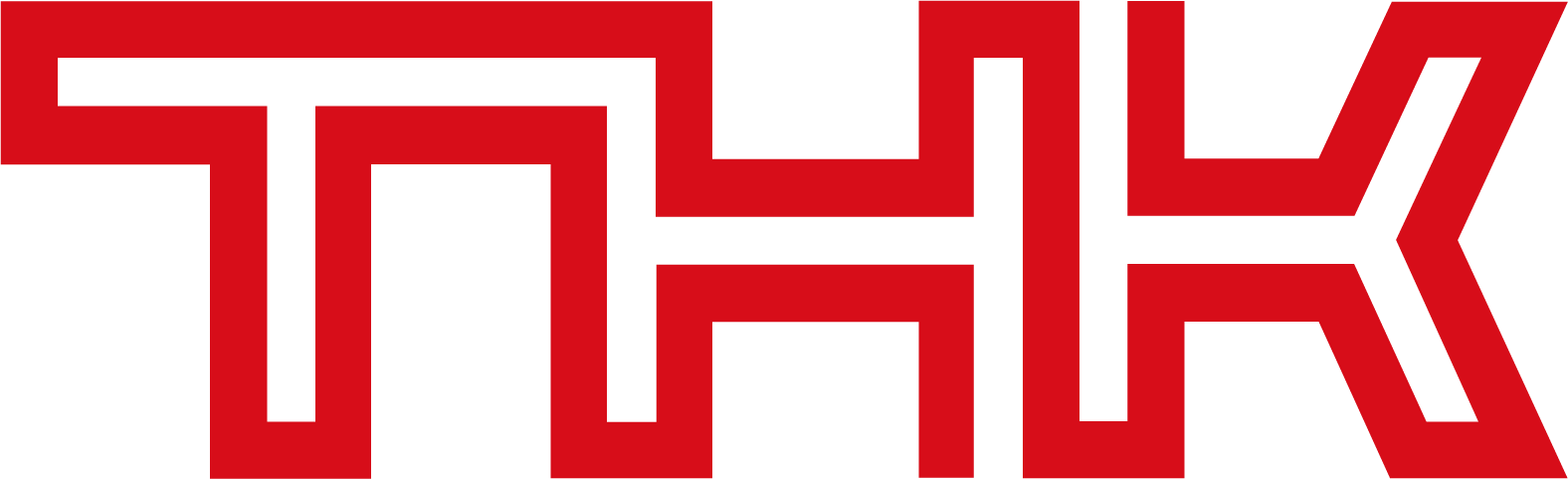
THK MANUFACTURING OF VIETNAM
Achieving 50% Reduction in Training Time Through Visual Work Standards – Building a Knowledge Foundation to Support Manufacturing Quality
THK MANUFACTURING OF VIETNAM, established in 2007 as the Vietnamese production base of THK Co., Ltd., the pioneer of linear motion guides, manufactures LM Guide and slide rails for industrial equipment such as machine tools, robots, and semiconductor manufacturing equipment. We interviewed them about the background and utilization of Teachme Biz, which was implemented to ensure correct procedures regardless of the operator in their inspection process, where high precision and quality control are essential.
- What led you to implement Teachme Biz?
Mr. Yoshida: With paper manuals, we struggled particularly with work instructions in the inspection process. While veteran workers have learned through experience how to “view from this angle,” “apply light this way,” or “use this much force,” these subtle operations couldn’t be effectively communicated through paper manuals, creating a significant barrier in training new employees.
Mr. Dung: Paper manuals presented numerous challenges. Finding the right manual was time-consuming, and different team members often interpreted procedures differently, leading to quality variations. Workers frequently needed to verify procedures with senior staff before starting work, which was time-consuming.
Mr. Yoshida: Updating procedures when improvements were made was another challenge. Timely updates were difficult due to the effort required for page replacement and retaking photos, resulting in procedural variations among workers.
Mr. Dung: Creating a single manual in Excel or PowerPoint took about 3 hours, plus the time needed for printing and distribution. When revisions were necessary, we had to collect old materials and redistribute new ones, which was also challenging to manage.
Mr. Yoshida: While we were discussing creating more comprehensible manuals incorporating videos, our Director introduced us to Teachme Biz. After seeing the demo, we decided to implement it, particularly impressed by its simplicity, clarity, and ability to record operations using images and videos.
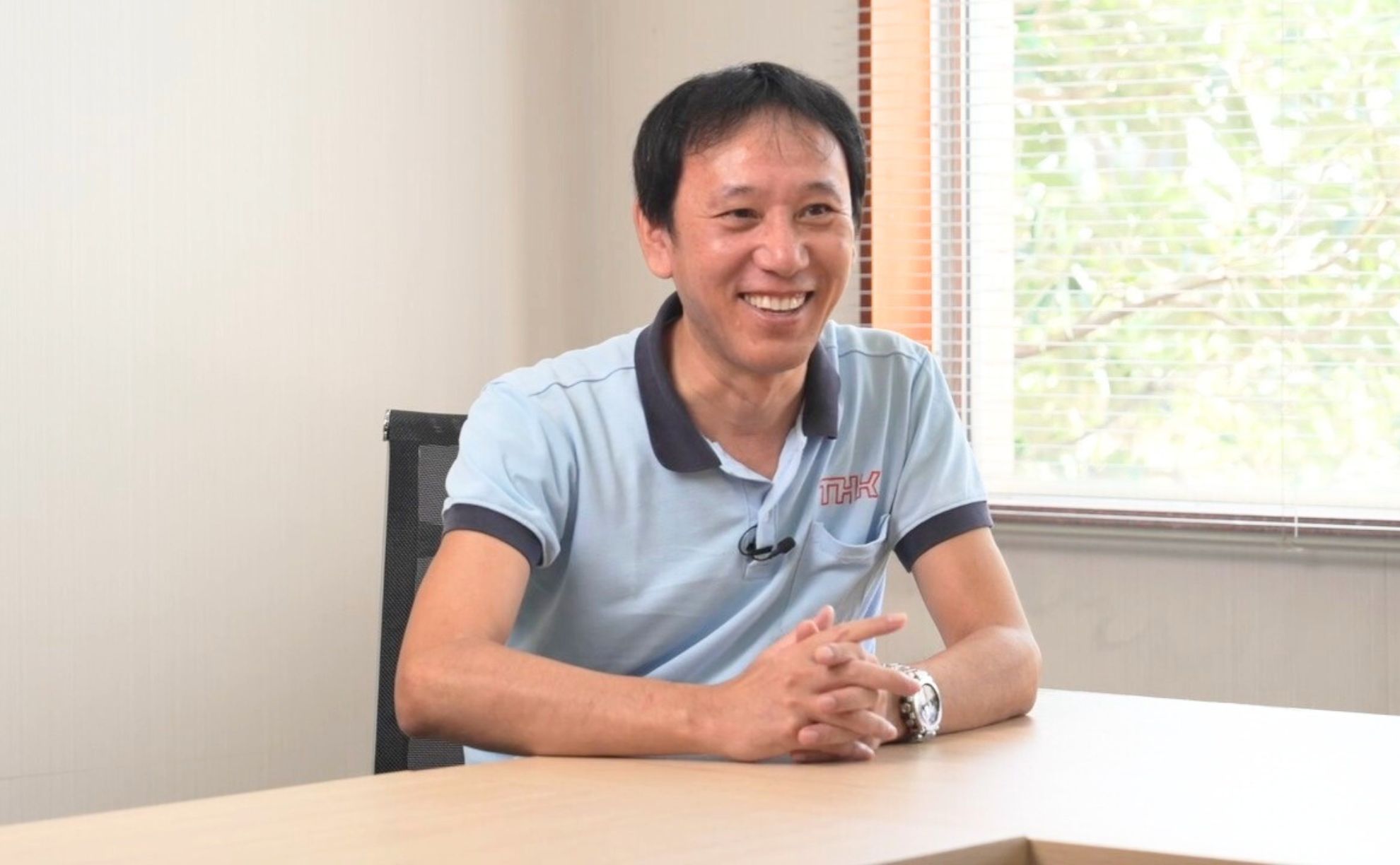
Mr. Yoshida, Quality Assurance General Manager
- In which specific operations are you using Teachme Biz?
Mr. Dung: We’re utilizing it in our final product inspection process. We attach QR codes to each product sample, allowing operators to instantly access inspection procedures specific to that product by scanning the code. We have a strict rule requiring workers to review the manual whenever they switch to inspecting a different product, ensuring they fully understand the unique inspection methods for each item. As a result, our operators reference these manuals daily.
Mr. Yoshida: When we first created the manuals, we had new employees use them and collected their feedback. We continuously incorporated specific improvement suggestions such as “this section needs more explanation” or “we’d like to see this motion demonstrated more slowly.” The system’s easy editing functionality has been crucial in enabling this continuous improvement process.
Feedback from new employees’ perspectives was particularly valuable in identifying areas where we had omitted explanations of things that seemed obvious to experienced workers. Through this iterative improvement process, driven by user feedback and enabled by the platform’s flexibility, we developed truly practical manuals that work effectively on the shop floor. This success in creating documentation that serves our operational needs made it easier to expand the system to other processes as well.
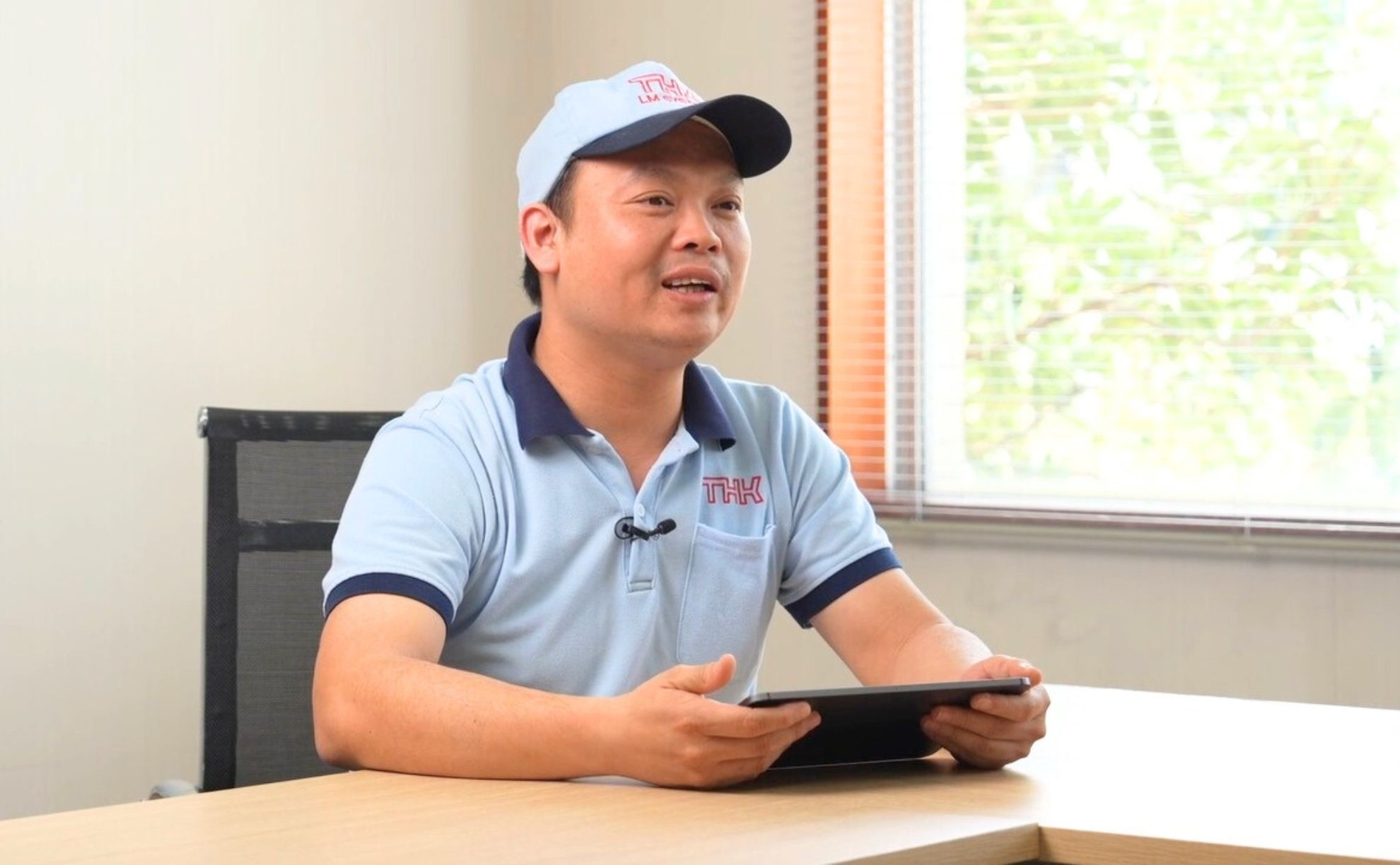
Mr. Yoshida, Quality Assurance General Manager
- How have the workers responded to using Teachme Biz?
Mr. Dung: The response has been overwhelmingly positive. Younger staff members, in particular, have adapted naturally to the system thanks to their familiarity with digital devices like smartphones. We often hear from new employees that they feel more confident because they can quickly verify any uncertainties they have.
Initially, some of our more experienced staff members expressed a preference for the familiar paper manuals. However, once they started using Teachme Biz, they discovered that it was not only easy to operate but actually more convenient than paper manuals. Now, even our veteran staff members appreciate how it helps them transfer their experience and know-how to younger employees more effectively.
Our workforce includes many Vietnamese employees, and we regularly have Japanese technical instructors visiting from Japan. Previously, even with interpreters, some nuances would get lost in translation. Since implementing Teachme Biz, the combination of videos and photos has helped us overcome language barriers, enabling accurate information sharing regardless of language differences.
The visual nature of the platform has proven to be a universal language that bridges communication gaps and ensures consistent understanding across our diverse workforce.
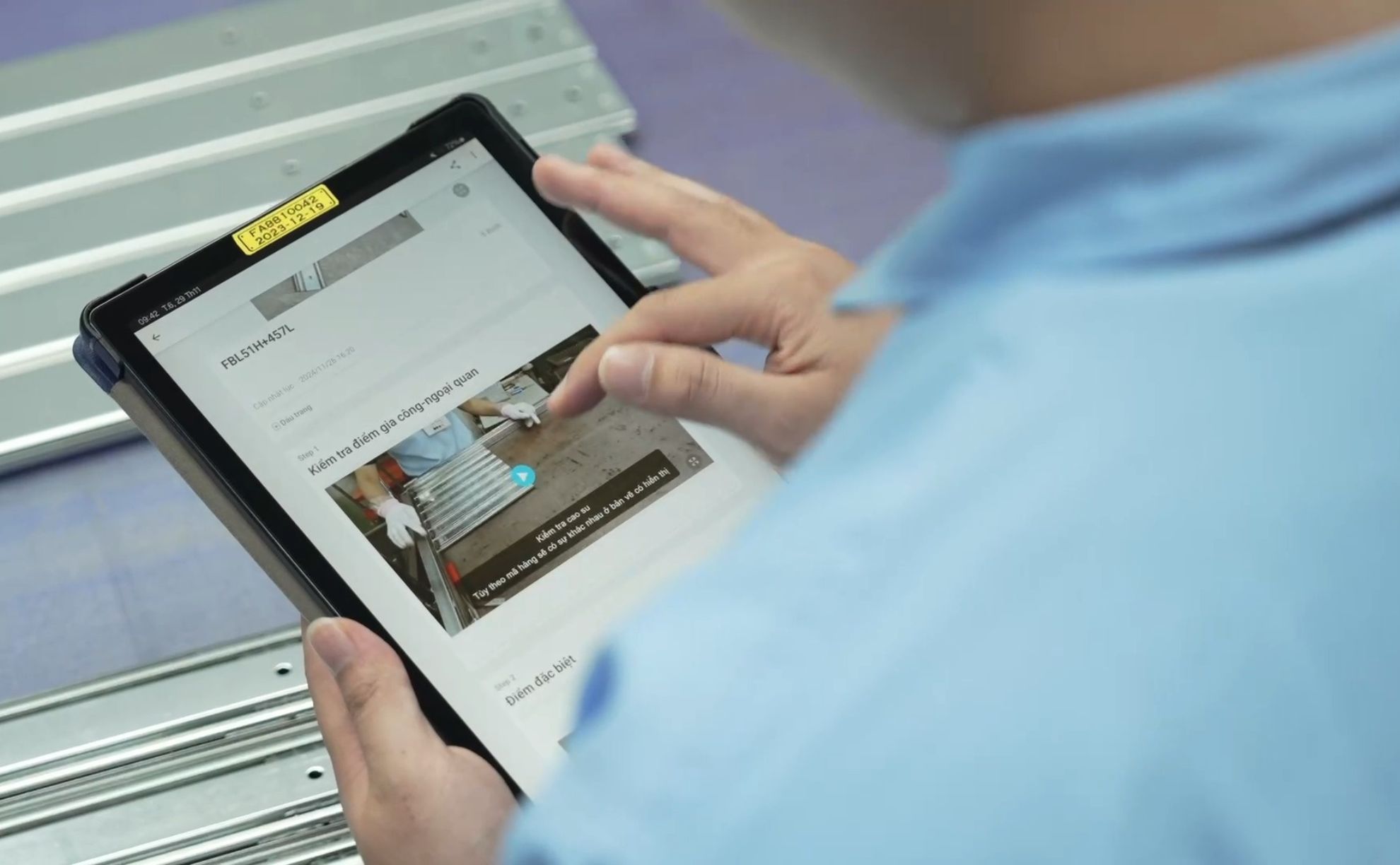
Mandatory procedure verification before inspection
- Could you tell us about the specific results and effects of implementing Teachme Biz?
Mr. Yoshida: After about six months of implementation, we’ve seen significant improvements in two key areas. First, we’ve achieved better quality through standardization of operations. With unified judgment criteria among operators, we’ve seen a substantial decrease in oversight of defective products.
Second, we’ve greatly improved the efficiency of new employee training. What previously took two weeks now only requires about a week. The ability to pause and replay videos has been crucial, allowing new operators to learn at their own pace. Additionally, the visualization of veteran operators’ techniques and know-how through videos has made it much easier to transfer tacit knowledge.
- Finally, what are your future plans for expanding the use of Teachme Biz?
Mr. Yoshida: Beyond our current use for work procedure documentation, we’re exploring broader applications. Specifically, we’re planning to create manuals for mold disassembly and assembly procedures, as well as documentation for equipment repair and maintenance methods. By recording equipment troubleshooting and periodic maintenance procedures on video, we aim to improve the quality of equipment maintenance and reduce downtime.
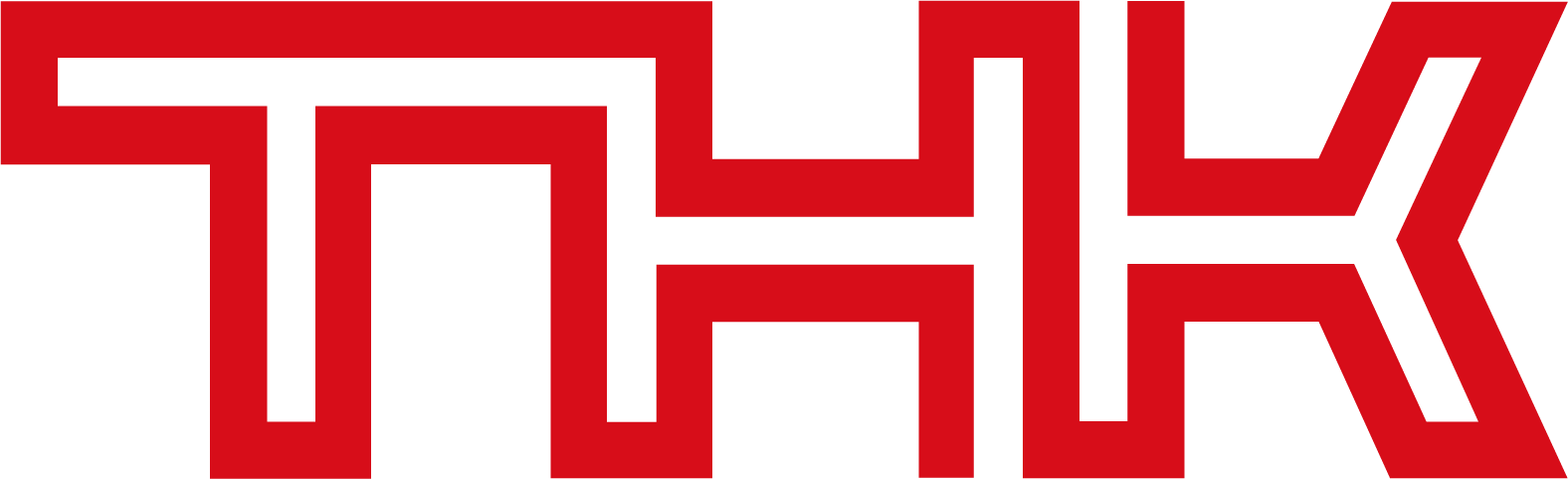
Company |
THK MANUFACTURING OF VIETNAM CO., LTD. |
---|---|
Website |
https://www.thk.com/jp/en/ |
Business Type |
Manufacturing and Innovative Services Company |
Business Detail |
LM Guide and Slide Rail |